You see it everywhere: car ads touting increased fuel economy, retailers featuring high-efficiency CFL light bulbs, and consumers carrying reusable grocery bags and coffee cups. The growing “green” movement encourages waste reduction to prevent over-burdening and polluting our natural resources.
As a manufacturer competing in the global marketplace, Leggett & Platt aggressively eliminates waste to reduce costs and provide more value to our customers. Our constant pursuit of efficiency naturally leads to more sustainable business practices. Our Geo Components business unit goes a step further by developing products engineered to protect the environment. Leggett has found that green businesses (and business practices) are good for business.
Using Trash to Save Cash
We pull most of our #1 raw material—steel—from the scrap heap, along with urethane foam, paper and other recyclables. Many Leggett businesses have found reused materials to be their most cost-effective source, and the Company diverts over a million tons of trash from landfills each year.
Davidson Plyforms discovered an innovative recycling solution when pressed to reduce the cost of its office furniture components by 40%. John Walton, Davidson’s President, said, “We initially looked at off-shore operations to make the parts, but the savings weren’t where we needed them to be.” Davidson’s break-through came from Innovative Resin Technology (IRT) that enables them to recycle multiple types of plastic waste without presorting them by category.
- The IRT process begins with bales of unsorted plastic trash.
- Davidson chops the plastic into a fine, even consistency.
- The Kinetic Energy Melter converts the material into a molten resin.
- The resin is cured and formed into a final product.
“With the extraordinary savings of time and energy from not separating the plastic before it’s melted down, we now have a nearly costless material source,” Walter explained. “The competitive advantage of IRT has boosted our bottom line and prevented us from outsourcing these components. Our employees and the reliability of our supply chain both benefit from this change.”
Lean Green Manufacturing
“Leggett stresses getting the maximum value out of every dollar, so it makes sense that we carefully manage our energy costs,” explained Steve Damer, Energy Services and Facilities Manager. “Improvements from our energy conservation program save us the equivalent of five million gallons of gasoline annually. We’re searching for additional savings every day.”
Our partners in Kendallville, Indiana, recently tackled an industry-wide initiative to improve the environmental profile of furniture manufacturers. The Kendallville team used the initiative’s guidelines and found annual savings of over $120,000 by modifying their tempering oven, reusing specialty-sized pallets, improving the facility’s lighting, and recycling lumber, plastic and paper.
Inspired by the success of our furniture group, Leggett’s Environmental and Continuous Improvement teams are launching the “ECO Initiative” at U.S. branches to boost profits by reducing waste. Instead of requiring specific changes, the ECO Initiative provides a flexible strategy that leverages the experience of partners at each location and borrows from the success of other operations. Lighting retrofits, low temperature metal cleaning, optimizing compressed air systems and other improvements will generate substantial savings.
Helping Others Help the Environment
Whether building homes, roads or skyscrapers, construction projects often create significant environmental problems. Government agencies may impose fines or delay projects if the issues aren’t properly addressed, so builders need a cost-effective response. John Dowdell, President of Hanes Geo Components, said, “We provide solutions ranging from filtration systems that improve water quality to geotextiles that extend the life of roads.”
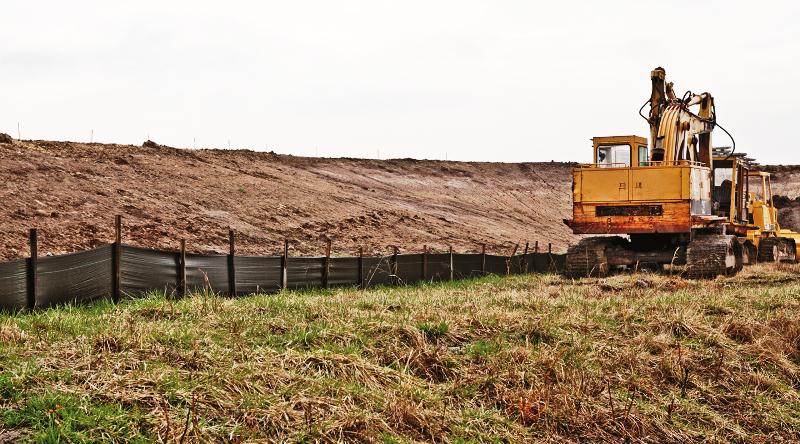
Since moving silt fence operations to the Winston-Salem facility in 2008, Hanes has produced enough fencing to circle the earth.
Headquartered near the rivers and forests of the Appalachian Mountains, Hanes knows the importance of preserving natural resources. The largest threats to the world’s fresh water supply are sedimentation and pollution from runoff. Sediment from construction projects can quickly turn a healthy body of water into a polluted mess.Fortunately, much of the damage can be prevented with silt fences—sturdy, woven fabric bound to a series of posts. These fences allow water to drain across the ground while keeping dirt and debris from reaching natural water sources. Hanes’ expertise in woven fabrics lent itself to silt fence production. After a series of investments to create efficient throughput, they quickly became North America’s leading producer.
“Federal regulation drives much of the demand, with silt fence installation being required at nearly every road construction site or real estate development,” Dowdell explained. ”It’s a simple, effective product that protects the environment and improves our bottom line.”
Rather than viewing environmental compliance as just another cost of doing business, Leggett is capitalizing on the green movement to grow our product offerings and improve profit margins. Consumers and governments are committed to sustainability, and we’re ready to do our part.
This article was originally published in the September 2011 issue of our semi-annual company magazine, InVision.