This National Safety Month, we’re proud to recognize the outstanding achievement of ECS Fort Smith in Fort Smith, Arkansas. With 193 (and counting) consecutive days without a recordable injury, the facility has achieved its longest injury-free streak since joining Leggett & Platt in 2019 – an accomplishment that reflects their unwavering commitment to putting people first.
Cristina Hassell, EHS Supervisor, credits this milestone to the relaunch of their safety committee, which has sparked a powerful shift in the culture.
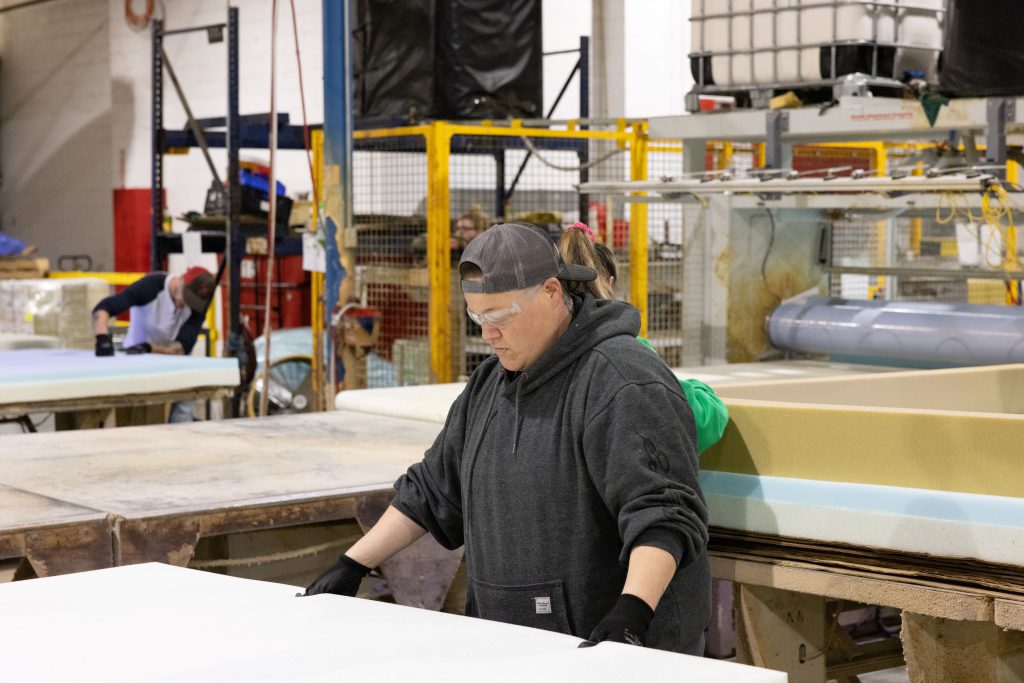
“There’s been a huge positive response,” says Cristina. “Our committee is engaged, hands-on, and focused. The leadership team has really stepped up to support safety across the board.”
Safety is woven into the daily routines at ECS Fort Smith. From daily safety meetings and weekly pop quizzes (with soda “pop” rewards) to recognizing safe work habits with T-shirts and actively involving employees in Job Safety Analysis (JSA) development, the team fosters ownership at every level. Monthly zone audits and peer-led new hire safety training reinforce consistent, proactive practices.
Overcoming complacency and shifting mindsets have been key challenges, but the team continues to raise the bar. In recognition of their achievement, they will receive a thank-you letter and an official safety award from branch leadership.
Congratulations to everyone at ECS Fort Smith for setting the standard and proving that safety starts with us!