At L&P, we’re inspired by our colleagues who go above and beyond to enhance our businesses. This month, we’re sharing stories of women at L&P who have improved our products and processes with their creativity and leadership.
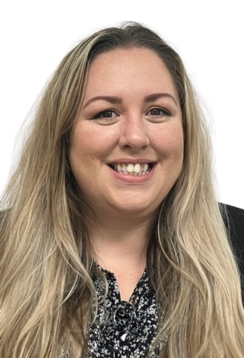
Meet Claire Jarvis! Claire has been with us for seven months and is a Quality Manager at our Aerospace branch in the United Kingdom. We asked her some questions about work and how she approaches problem solving.
What is a day at work like for you?
A typical day in my role consists of managing my branch’s workload and supporting business processes to achieve customer satisfaction.
How have you improved L&P processes and products?
I’ve updated some of our core operating procedures, led our business through a BSI AS9100 audit, and supported special process owners through a NADCAP (National Aerospace and Defense Contractors Accreditation Program) audit. We also recently changed our approach to non-conforming products, introducing a triage process to effectively determine the root cause.
AS9100 – for the Quality Management System – enables us to continue shipping products with a AS9100-certified certificate of conformance. We hold NADCAP approval for welding and NDT (nondestructive testing). Both of these audits are beneficial because they ensure we’re working within stringent requirements, and these standards are recognized by our customers and industry as being at the height of best practice.
How do you approach problem solving?
I ensure the problem is clearly identified. It can be easy to assume what the problem is, which could lead to ineffective solutions. Also, I work as part of a team! We all have different strengths, and by working collaboratively, we can pull on each other’s strengths and find robust solutions.
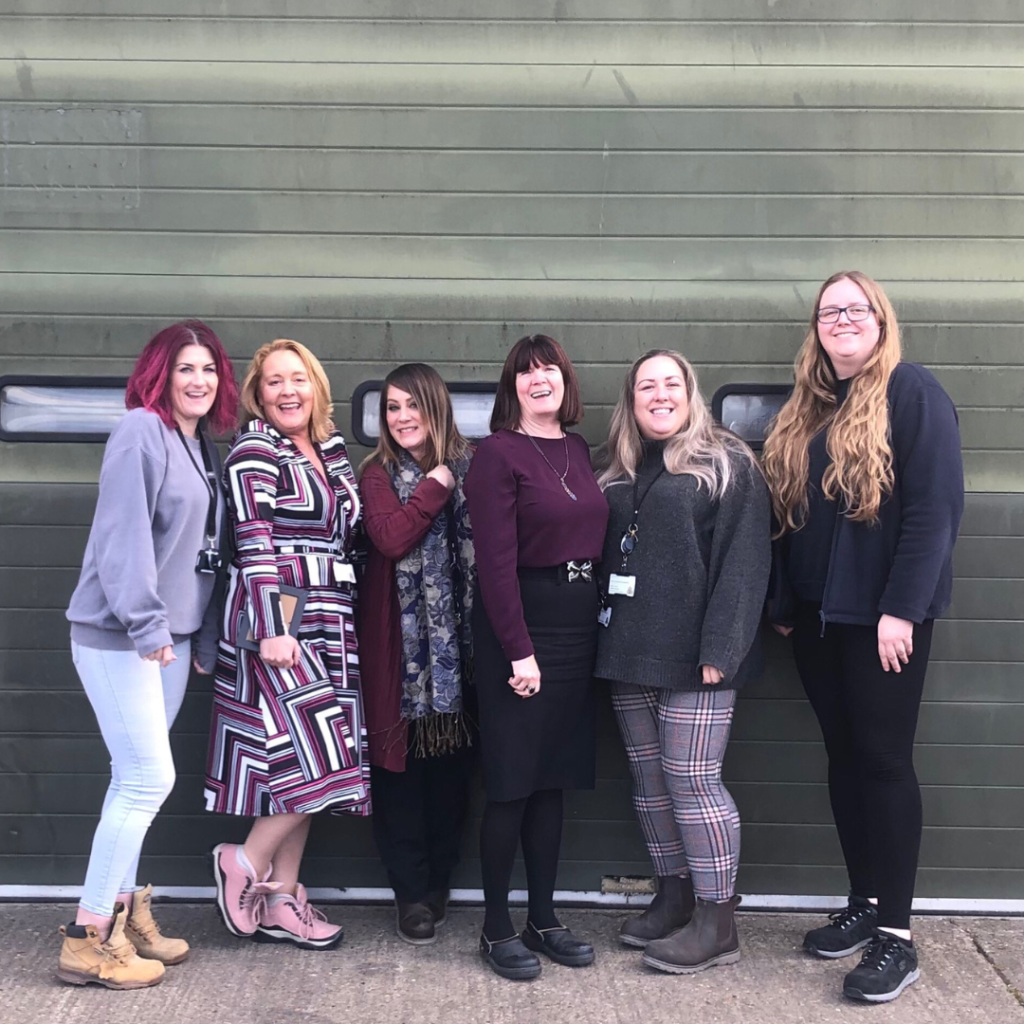