As one of our core values, Continuous Improvement affects everything we do at Leggett & Platt. According to CEO Karl Glassman, “The potential for ingenuity is present in every business unit, facility, and position here at Leggett & Platt. We’re all counting on one another to keep improving and keep looking for a better way.”
For the team at Winchester Spring, finding a better way has certainly paid off.
Starting a Lean Pilot Program
Several years ago, the Bedding Group recognized a need to improve our competitive position, increase profits, and retain valuable employees. Eric Rhea, President of the Bedding Group, proposed an initiative for a lean pilot program, and Winchester Spring in Winchester, Kentucky volunteered to be the first to participate.
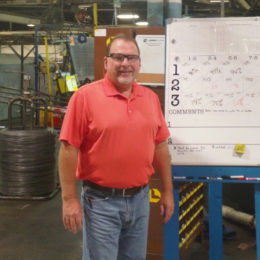
Chuck Denisio
According to Chuck Denisio, Branch Manager, “The idea of implementing lean tools really complemented everything we’d been trying to accomplish at Winchester. I raised my hand because I wanted to get in at the ground floor of something new and exciting.”
Howard DeCelis, Staff VP of Continuous Improvement, was charged with starting the lean program at Winchester Spring. A lean program, just one of many continuous improvement methods, is the systematic process of identifying and eliminating waste. So, in 2016, a cross-functional Corporate team and a small team at Winchester began to do just that.
After overview training and employing basic tools and principles, they found numerous areas of opportunity. Howard admits, “We quickly learned that we exposed more problems than we had resources to address them.”
Numerous Projects = Numerous Cost Savings
One early success was a project involving the setup of new, complex, and expensive PA494 machines, which produce the Quantum Edge Comfort Core mattress. A team led by Brian Hill, Caleb Winburn, and Richard Trent underwent a four-day process of observation and analysis to determine how to save time with machine setup.
They utilized a lean tool called a SMED (Single-Minute Exchange of Dies), which is a system for drastically reducing the time it takes to complete equipment changeovers. The result of the SMED was a 67% reduction in hours worked to set up the machines, which added additional production capacity due to reduced time performing changeovers.
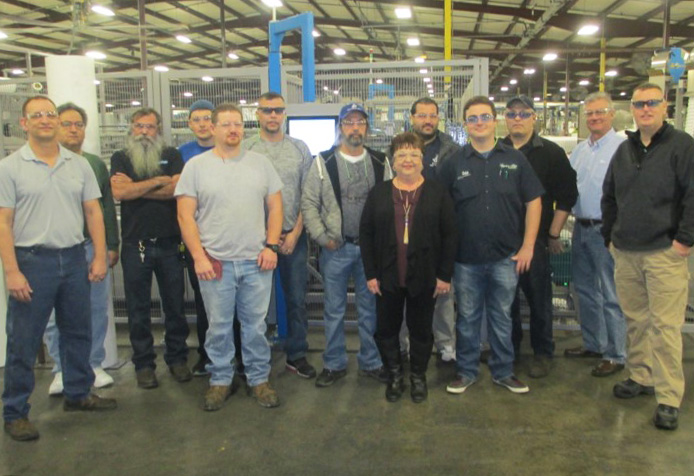
The SMED team for the PA494 project.
Another recent win came after the branch had received customer complaints about mis-tagged mattresses. As part of the lean program, Howard sent a team for a Rapid Continuous Improvement (RCI) event, which is a 4-day workshop of intense focus. They analyzed step-by-step how the products moved through the tagging process. “We looked at man, machine, materials and method,” says Howard, “and we brainstormed every possibility that could go wrong with correctly tagging the product, then targeted and eliminated those possibilities.”
The result was a huge win. Since “mistake-proofing” the tagging process, the branch hasn’t received any additional complaints.
The team at Winchester hopes for more success stories to come. “This lean program has been so good for our branch,” says Chuck. “The opportunities for future improvement are endless, and that’s been my drive. Change is not optional. If you don’t change and you don’t improve, you’ll get left behind.”